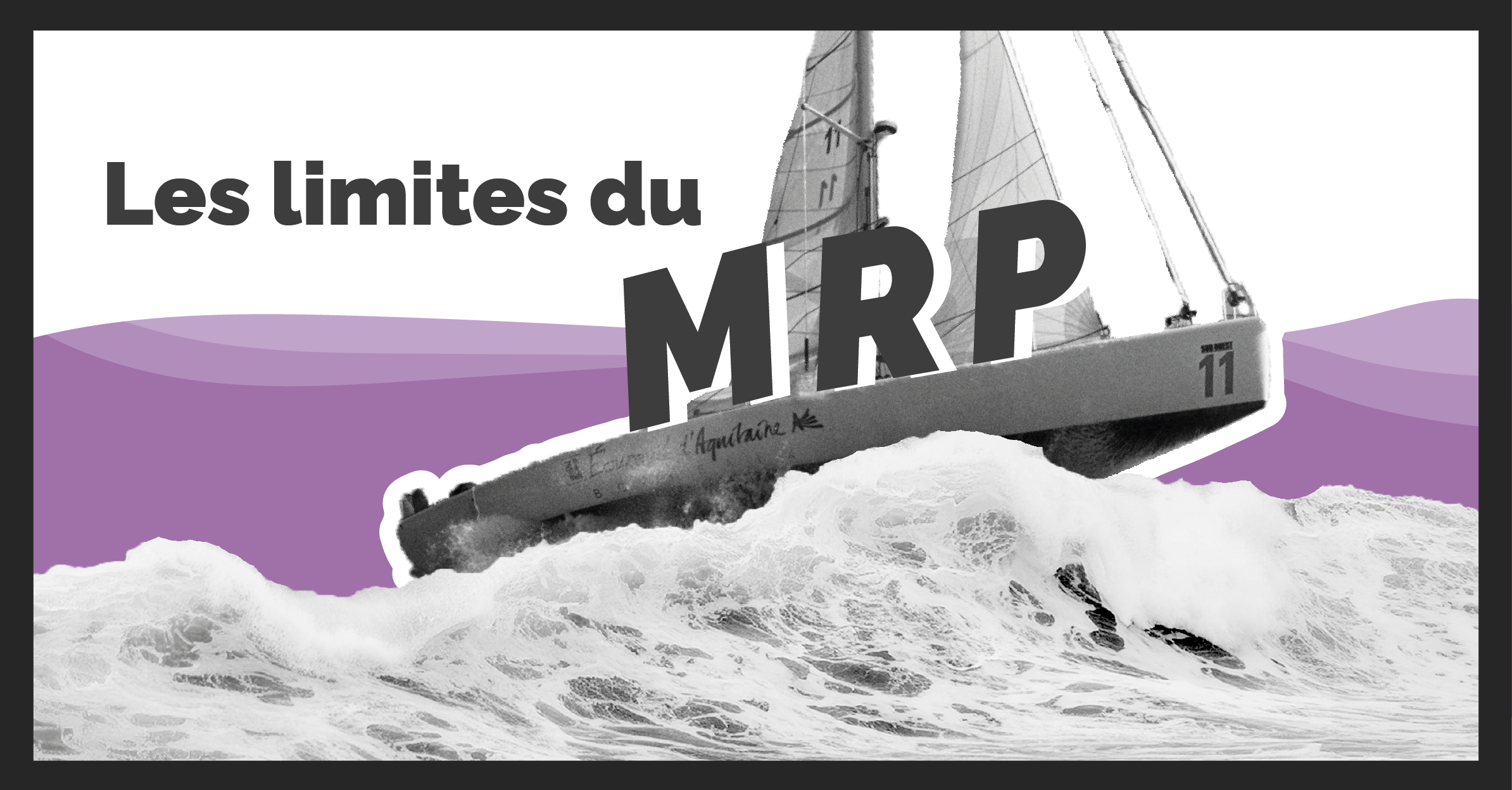
Naviguer dans l’incertitude : le MRP à l’épreuve du monde VUCA. Le MRP, boussole des industriels d’antan, peine à guider les Supply Chain dans la tempête du monde moderne. En proie à des changements incessants et des événements imprévus, les entreprises doivent repenser leurs outils de planification pour survivre et prospérer. Cap sur les limites du MRP et les nouvelles solutions.
Déroulé de l'article
Rappel : qu’est-ce que le MRP ?
1. Les origines du MRP
Le MRP c’est LA méthode de calcul des besoins certainement la plus utilisée encore aujourd’hui. Née dans les années 1960 avec Joseph Orlicky, elle part des prévisions de ventes sur les niveaux produits finis et remontre les nomenclatures pour déterminer :
- Ce qu’il faut produire
- Pour quand
- Et en quelle quantité
Depuis, des évolutions du MRP ont vu le jour avec par exemple la notion d’adéquation charge – capacité pour contrôler la faisabilité du planning de production.
Le MRP reste une méthodologie de planification “en flux poussé”. Les stocks de produits finis sont poussés par les prévisions. Et tout est fait pour que les composants soient disponibles pour la fabrication de ces produits finis.
2. Les hypothèses (dépassée) du MRP
Ce calcul de besoin MRP a prouvé par le passé qu’il fonctionnait, puisque les industriels réussissent à servir leurs clients. Mais sur la base de quelles conditions ?
À l’instar des navigateurs affrontant les tempêtes et les icebergs, les industriels d’aujourd’hui naviguent dans un monde VUCA (Volatil, Incertain, Complexe et Ambigu). Le calcul des besoins MRP, bien que pertinent dans un environnement stable, peine à s’adapter à ces réalités mouvantes.
En effet, “stable” n’est pas l’adjectif qui décrit le mieux le monde d’aujourd’hui. Est-ce qu’un approvisionneur, un planificateur ou un ordonnanceur vivent un long fleuve tranquille au quotidien ? Pas vraiment… crise financière, COVID, crise énergétique, guerre en Ukraine, pénurie de transport… les crises s’encenchaînent impactent les Supply Chain.
Les industriels sont les navigateurs d’aujourd’hui. Autrefois, les courses comme le Vendée Globe se déroulaient sur des tracés classiques. Aujourd’hui, les navigateurs doivent composer avec la dérive des glaciers, les changements de courants… Leur bateau et leur plan de navigation doivent être flexibles s’adapter en permanence.
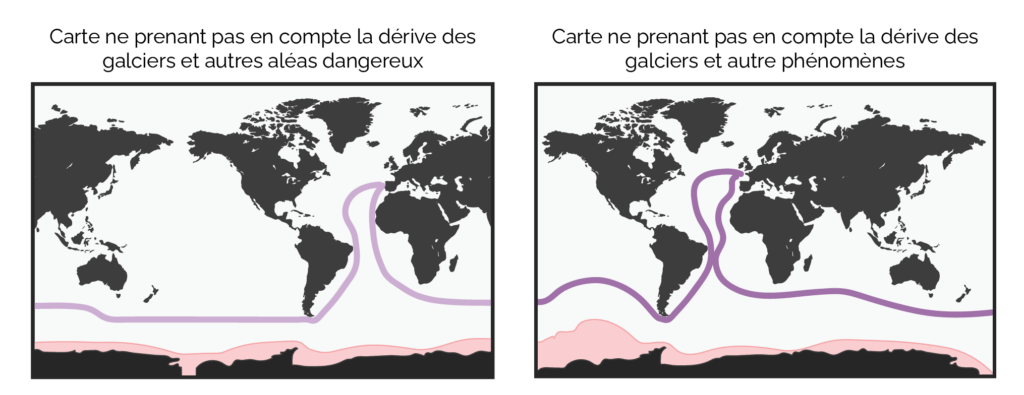
Autre point, la confiance aveugle dans les prévisions pour piloter la production avec le modèle MRP. Par essence, une prévision est incertaine. Même dopées par l’IA, ces prévisions restent des approximations imparfaites, d’autant plus dans un environnement instable. Imaginons un navigateur se basant uniquement sur des cartes marines statiques pour affronter une tempête !
Mais alors, baser les planifications de production sur les prévisions est-ce vraiment raisonnable ?
Nous vous conseillons de lire l’article « Les Supply Chain dans le monde VUCA?« si vous voulez comprendre cet environnement instable
Les effets du MRP dans les Supply Chain actuels
1. Trop de sur-stocks ET de sous-stocks
Et oui les deux à la fois… Nous venons de le voir, le calcul de besoin MRP est basé sur les prévisions. Mais si les prévisions sont trop éloignées de la réalité, le résultat sera… pas vraiment optimal…Dans notre langage de consultants (issu des statisticiens), nous parlons de “répartition bimodale des stocks” , ce qui veut dire que si on regarde la couverture de stocks de l’ensemble des articles, on va trouver :
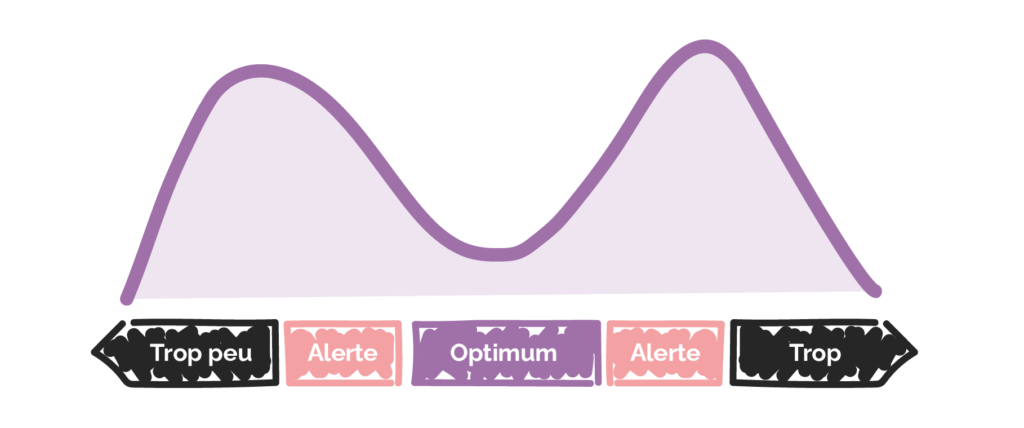
- Un 1er pic (ou 1er mode) avec beaucoup d’articles dont le stock est trop faible par rapport à la demande. La prévision a sûrement été sous estimée. Des sous-stocks, c’est une potentielle perte de CA, des clients qui peuvent aller voir chez vos concurrents, de l’énergie dépensée (et de l’argent dépensé) pour chercher des solutions alternatives (transports express, heures supplémentaires etc.)…
- Un 2ème pic (ou 2ème mode) avec beaucoup d’articles dont le stock est trop élevé par rapport à la demande. Certainement une prévision surestimée. Des sur-stocks, c’est de l’argent immobilisé, de la place monopolisée dans un entrepôt, des risques d’obsolescence…
- Et au milieu de tout ça, très peu d’articles avec juste ce qu’il faut en stock
Tout ce que nos amis vendeurs adorent…Et le meilleur dans tout ça, c’est qu’un même article peut osciller entre ces 2 modes au cours du temps. Un mois en sous-stock, l’autre mois en surstocks. Suite à une rupture, l’approvisionneur qui s’est fait taper sur les doigts va avoir tendance à en recommander bien trop pour se couvrir…
2. Trop de messages contradictoires et de changements au quotidien
Le MRP va chercher à ce que les composants arrivent pile au moment où ils sont demandés, en visant un stock de 0. Tous les OF sont donc synchronisés entre eux à la date près. Ce qui signifie que le moindre changement d’une date va générer en cascade des changements, pour les OF en amont et/ou en aval dans la nomenclature. Donc tout fonctionne bien tant que ces changements restent stables. Sauf que… nous l’avons vu dans l’article précédent, le monde industriel d’aujourd’hui est tout sauf stable.
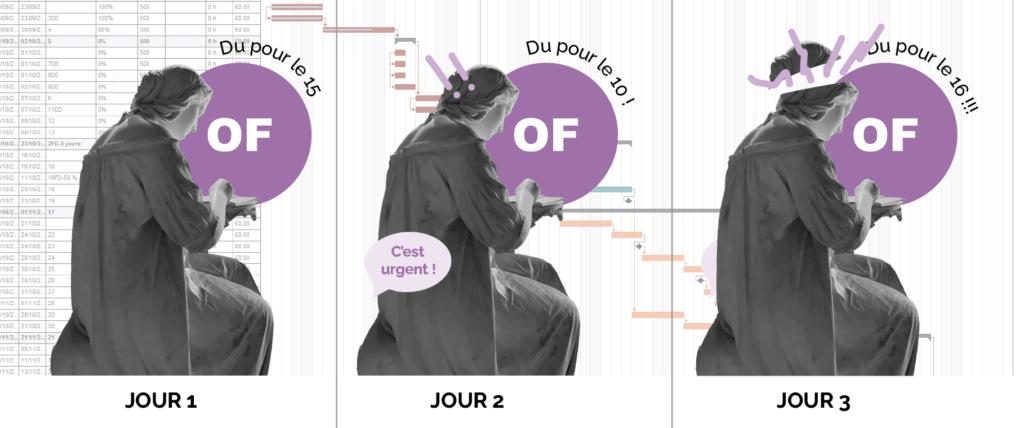
Les planificateurs se retrouvent alors à traiter chaque jour des messages dans leur ERP, comme par exemple :
- “l’ordre d’approvisionnement / de fabrication doit être avancé”
- “l’ordre d’approvisionnement / de fabrication doit être reculé”
Il y en a tellement que ça en devient difficile de tous les traiter chaque jour. Ce phénomène entraine aussi une frustration des planificateurs à reculer un OF un jour, avant de devoir l’avancer quelques jours plus tard.
Mais ces changements incessants peuvent également agacer clients et fournisseurs. Les clients ne comprennent plus à quelle date ils seront réellement livrés. Les fournisseurs ne comprennent plus à quelle date ils doivent finalement livrer.
3. Une amplification de l’effet coup de fouet (bullwhip)
Imaginez un navire en mer, guidé par un cap fixé sur la carte. Si le vent change légèrement de direction, le navire déviera légèrement de sa trajectoire de quelques mètres. Mais si ce changement de direction se répète tout au long du voyage, l’écart final par rapport au cap initial peut devenir considérable et se compte en kilomètres.
C’est l’effet « coup de fouet » en planification MRP. Une petite variation de la demande au niveau des produits finis, semblable à une légère brise, va se propager et s’amplifier tout au long de la chaîne d’approvisionnement, comme des vagues qui se renforcent en mer.
La variabilité en planification MRP c’est un peu pareil. S’il y a une petite variation de la demande au niveau des produits finis, elle va se propager (en étant amplifiée) jusqu’aux matières premières, et en passant par les nomenclatures. C’est l’effet coup de fouet. Un petit changement de plus ou moins 10 pièces au niveau de la demande finale, peut se transformer en un plus ou moins 100 pièces au niveau du fournisseur à l’autre bout de la chaîne.
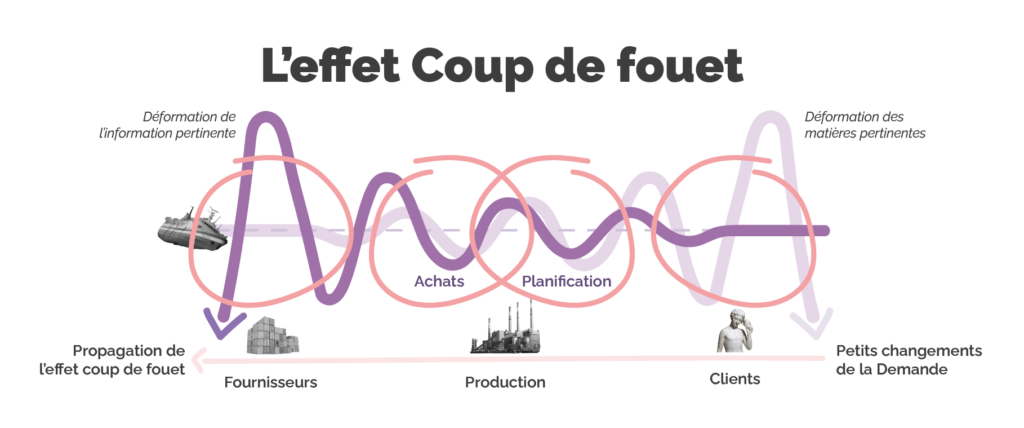
Pourquoi ce petit nom d’effet coup de fouet ? Imaginez une corde ou un fouet au sol, que vous agitez de haut en bas à une extrémité. Vous allez créer des « vagues », qui, vont être d’amplitude faible à l’extrémité que vous agitez, et d’amplitude bien plus grande à l’extrémité libre de la corde. Plus le fouet va être long, plus la différence d’amplitude va être importante. Soit, si on revient à nos Supply Chain industrielles, plus il y a de niveaux dans la nomenclature, plus la variabilité au début de la chaîne va augmenter…
À noter que ce phénomène est également valable avec un réseau de distribution entre la demande du client finale dans un point de vente et les fabricants
Vers une évolution du MRP ?
Vous vous reconnaissez dans ces phénomènes ? Si ça peut vous rassurer, vous n’êtes pas une exception et il existe des moyens d’y faire face ! C’est face à ces constats sur le MRP qu’est apparu le DDMRP. Même si ce n’est pas LA baguette magique qui va résoudre toutes les problématiques des Supply Chain, la méthodologie apporte déjà plus de réponses que le MRP. Et combiner le DDMRP à d’autres méthodes, aussi bien opérationnels (lean, rituels etc.) que stratégiques (S&OP), permet d’obtenir des résultats très intéressants.
À l’image du Véndée Globle, il paraît inimaginable de courir en 2024 avec le même bateau vainqueur de 1989. Tous les skippers préféreront utiliser un voilier embarquant les dernières innovations pour faire face à toutes les tempêtes et les imprévus pour maximiser leurs chances de remporter la course !