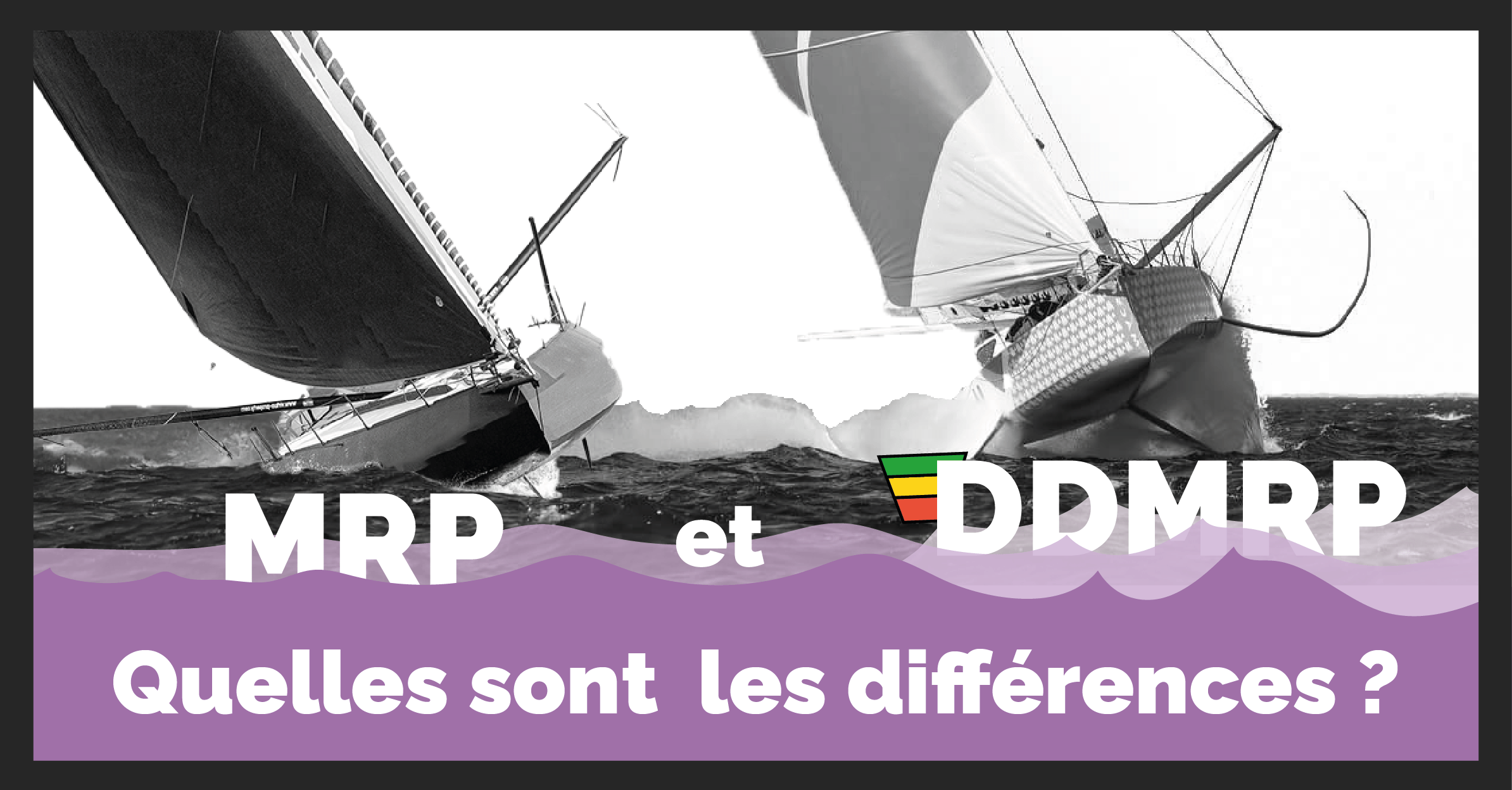
Plongez dans l’univers de la planification Supply Chain en comprenant les différences fondamentales entre le DDMRP et le MRP : gestion des stocks, prévision de la demande et absorption de la variabilité.
Déroulé de l'article
La planification correspond à la génération des ordres de fabrication (OF) et des ordres d’achats (OA). Ces ordres permettent soit de recompléter le stock d’un article (on parle alors de MTS pour Make To Stock) ou de répondre à une demande client (un MTO ou Make To Order).
Pour réaliser cette planification, les industriels peuvent s’appuyer sur plusieurs méthodologies : MRP, Kanban ou encore DDMRP pour ne citer qu’elles. Concentrons nous aujourd’hui sur le MRP et le DDMRP : à part deux lettres d’écarts, quelles sont les principales différences entre ces deux méthodologies ?
Les méthodes de planification en Supply Chain
Le MRP ou CBN : la méthode de planification la plus répandue
Le MRP (Materials Requirements Planning), aussi appelé CBN en France (Calcul de Besoins Nets) est certainement la méthode de planification la plus répandue dans le monde industriel. Apparu dans les années 1960, elle a su s’imposer pour devenir le moteur de calcul qui se cache derrière la plupart des ERP encore aujourd’hui.
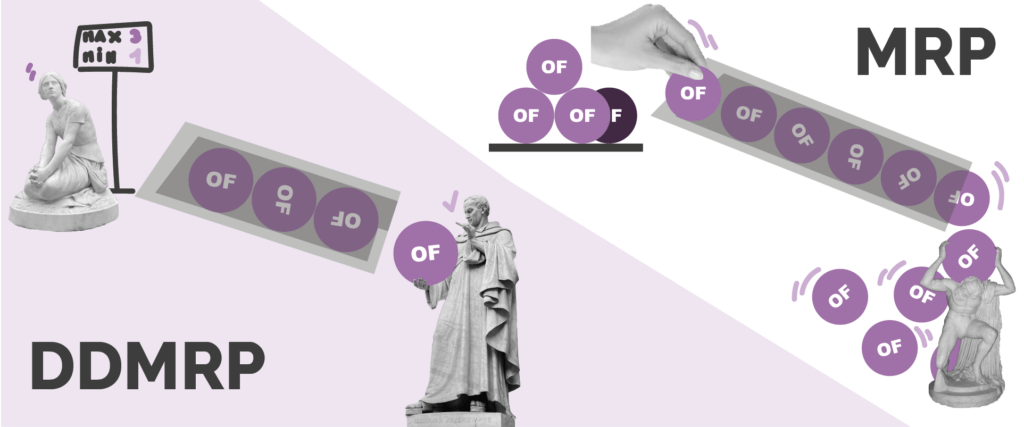
Le DDMRP : la méthode de planification qui se démocratise
Face au constat que le monde d’aujourd’hui ne ressemble plus au monde des années 60, une nouvelle méthodologie est apparue dans les années 2000 : le DDMRP (Demand Driven Materials Requirements Planning). Elle est basée sur le MRP (la preuve son nom a gardé cet acronyme), le DRP (Distribution Requirements Planning), le Lean/Kanban, la théorie des contraintes ou encore le 6sigma. Bref, elle reprend le meilleur de tous ces concepts.
MRP vs DDMRP : les 3 grandes différences
1. Le signal de demande qui déclenche un réapprovisionnement
MRP : les prévisions qui déclenchent les réapprovisionnements
Pour calculer les besoins bruts de réapprovisionnements de chaque niveau de nomenclature, la méthodologie prend en compte les commandes clients mais également les prévisions de chaque article. Mais les prévisions, par définition, c’est faux…
Les industriels se retrouvent donc avec un planning de production potentiellement rempli d’articles qui vont finalement dormir des jours, ou même des mois sur les racks. A contrario, si une demande client tombe sur un article non prévu, impossible de le glisser en production.
Le symptôme classique est qu’à la fin, on se retrouve avec une répartition dite bimodale des stocks : beaucoup d’articles en ruptures et en même temps beaucoup d’articles en surstocks. Ce qui ne plait ni aux commerciaux, ni aux financiers…
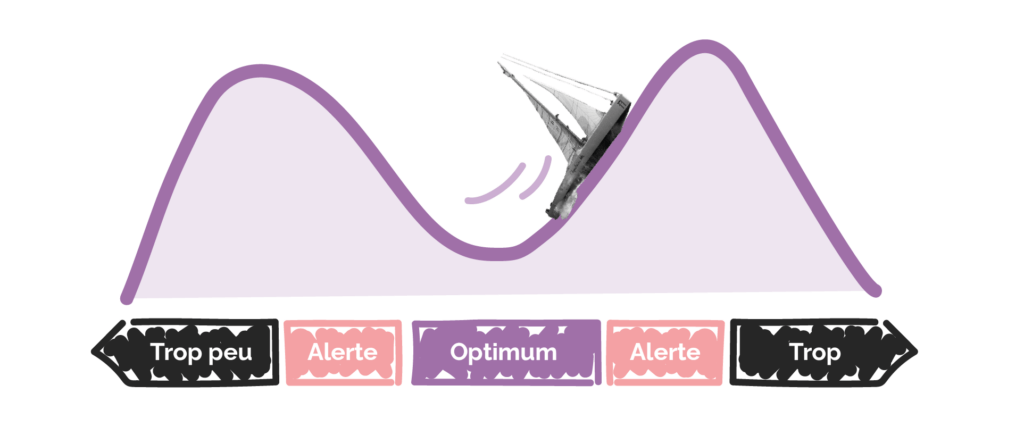
DDMRP : la demande réelle qui déclenche les réapprovisionnements
Tant qu’il n’y a pas de demande ferme enregistrée dans l’ERP, la méthodologie ne propose pas de nouveau réapprovisionnement. On ne monopolise pas l’atelier de production avec des articles qui vont servir “à rien”.
Mais attention, cela ne veut pas dire que les prévisions ne servent plus à rien dans un environnement flux tiré. Elles sont juste utilisées autrement. Les prévisions peuvent par exemple intervenir dans le dimensionnement de vos niveaux de stocks.
Les prévisions peuvent aussi permettre de faire des projections de charge : à partir d’une prévisions sur les produits finis, les outils remontent les nomenclatures et simulent les ordres d’achats / fabrication à chaque niveau.
Pour reprendre l’exemple d’une course de voiliers (cf article précédent). Si les concurrents ont tous pris le soin d’analyser les prévisions météo et de tracer un plan de navigation prévisionnel, aucun d’entre eux ne sera capable de le suivre à la lettre. Les conditions de navigation réelles, les anticyclones qui n’auront pas été prévus par exemple, vont les obliger à dévier du trajet initial.
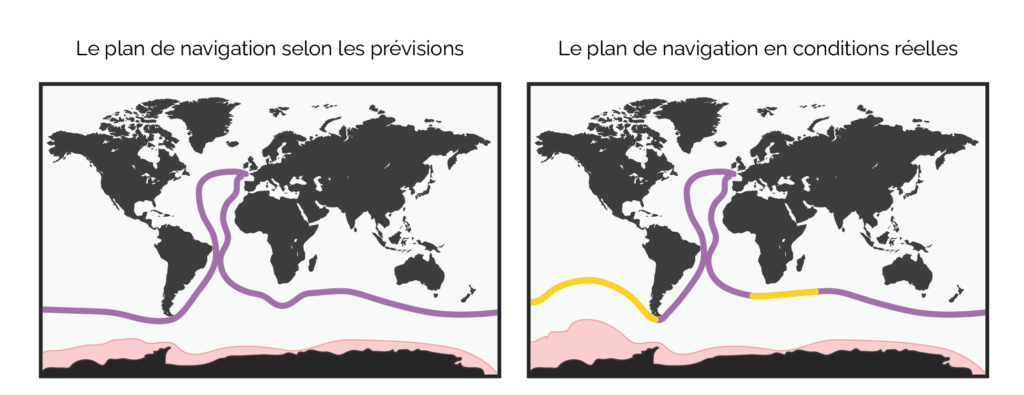
2. L’absorption de la variabilité (urgence & bullwhip)
MRP : il atténue partiellement la variabilité
Au départ, la méthodologie MRP vise les stock à 0 pour chaque niveau. Mais les stocks de sécurité ont poussé comme des champignons pour, en théorie, absorber les aléas. Dans les faits, ces stocks de sécurité MRP atténuent les aléas en direction des clients (à condition que les niveaux soient actualisés régulièrement…) : je mets des stocks pour m’assurer de toujours pouvoir servir mes clients même si ma production ne suit plus.
Mais du coté des fournisseurs c’est une autre histoire (c’est le fameux phénomène bullwhip). Le fonctionnement des alertes sur le stock de sécurité est assez binaire : soit mon stock est tout au dessus et tout va bien, soit mon stock a pénétré le stock de sécurité et l’ordre de réapprovisionnement est considéré comme urgent de suite. Toute la chaîne de production en amont est alors mise en alerte et l’alerte s’amplifie de niveau en niveau… jusqu’au fournisseur.
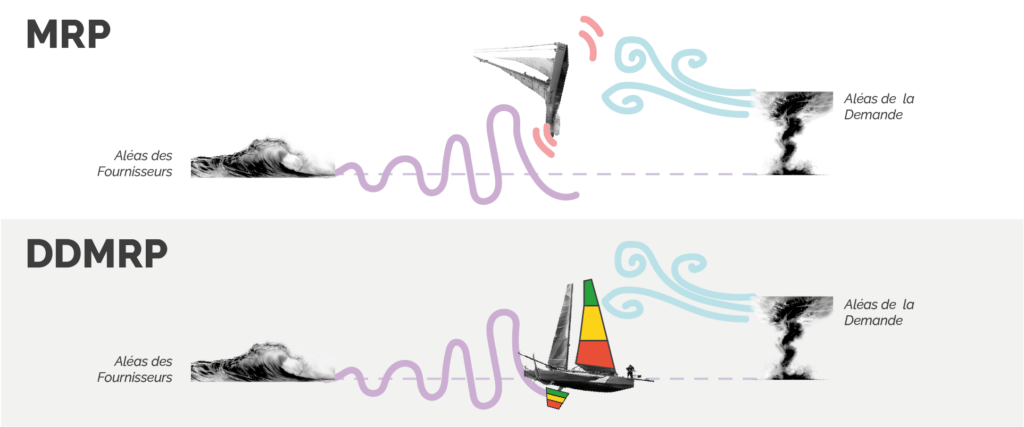
DDRMP : il joue un vraie rôle de point de découplage
En flux tiré, la méthodologie DDMRP reprend les éléments de base tout en allant plus loin. Le principe de mettre des stocks de sécurité est transformé en buffers de stocks (”stocks tampons” en français) aux endroits stratégiques de la Supply Chain. Mais avec 2 différences majeures sur son dimensionnement et l’absorption de la variabilité.
- Ces buffers de stocks s’actualisent tous les jours.
- Leur dimensionnement peut évoluer si la consommation est par exemple à la hausse ou à la baisse.
Mais le point majeur se situe autre part : un buffer de stock est divisé en 3 zones : verte jaune et rouge. On peut alors prioriser la criticité de chacun des stocks. Si le stock est dans le vert tout va bien. Mais plus on va entamer la zone jaune puis la rouge rouge, plus ça va devenir critique. Un message clair peut donc être partagé aux fournisseurs concernant le degré d’urgence et de priorité de chaque article.
3. Le dimensionnement des stocks
MRP : nécessite des revues régulières et manuelles des stocks de sécurité
La méthodologie MRP est vraiment axée sur le calcul des besoins. Il se fait notamment à partir du stock actuel des articles et des éventuels stocks de sécurité renseignés. Mais, le MRP ne prévoit pas de revue de ces stocks de sécurité.
C’est très souvent un point qui pêche chez les planificateurs & les approvisionneurs. Combien d’entre eux sont capables d’affirmer que les stocks de sécurité sont réactualisés au moins 1 fois par an ? Très peu. Une fois tous les trimestres ? Encore moins… Il est courant d’entendre “on les a calculé au démarrage de l’ERP, et ça s’est arrêté là”.
Pourtant les consommations de chaque article ont du changer depuis le temps. Les stocks de sécurité ne sont plus adaptés. Comment générer des ordres d’achat ou de fabrication avec des “bonnes quantités” (selon ce qui est vraiment nécessaire ou pas) à partir de données fausses…
DDMRP : propose un dimensionnement de stock dynamique et automatique
À contrario, la planification en flux tiré ou DDMRP, couvre cette aspect.
Si l’article a assez de consommations, il est définit en “buffer”. C’est à dire qu’on lui affecte un stock tampon. Ce stock va alors être défini à partir de trois zones : rouge, jaune et vert. Mais le grand changement, c’est surtout que ces 3 zones sont dynamiques : elles dépendent (entres autres !) de la consommation moyenne journalière de chaque article.
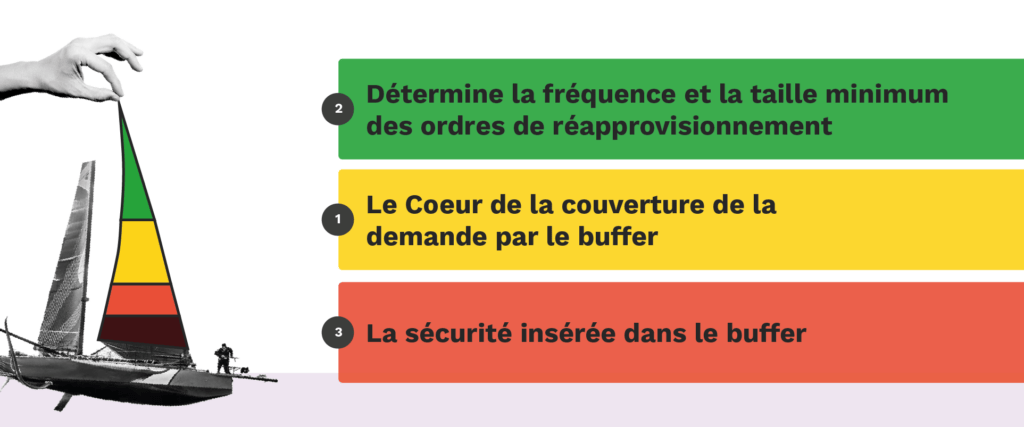
La planification en flux tiré vous intéresse ? Découvrez nos formations et Serious Game pour appréhender les fonctionnements des buffers de stocks
Dès qu’on importe un nouvel historique dans l’outil (ce qui est fait à minima 1 fois par jour), la consommation moyenne va être recalculée et le dimensionnement du buffer également. Donc si l’article est de plus en plus consommé, son stock va petit à petit augmenter lui aussi. Et inversement, si la consommation de l’article baisse, son stock va aussi diminuer.
Mécaniquement les buffers vont se mettre à jour. Une épine en moins pour les planificateurs & approvisionneurs. Ils vont pouvoir se concentrer sur des tâches à plus grande valeur ajoutée ! Ceci dit, le DDMRP inclut également une revue du paramétrage des stocks pour s’assurer que les 2 zones sont bien dimensionnées : si on a passé trop de temps dans le bleu, peut être faut-il diminuer les zones, ou inversement si on a passé du temps dans le rouge, peut être faut-il l’augmenter ?
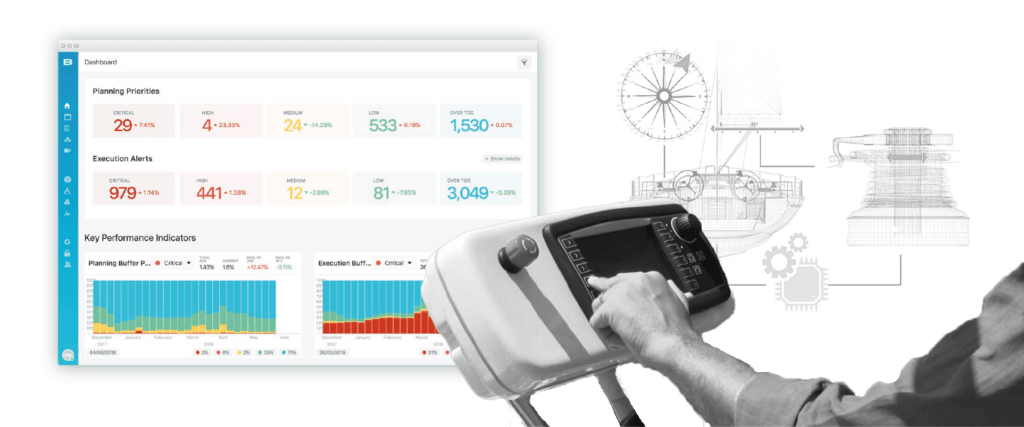
Reprenons l’exemple d’un voilier : sur un voilier classique, le skipper doit sans arrêt régler ses voiles (en plus de pleins d’autres choses à faire !). On appelle ça border ou choquer la voile. Si il ne détecte pas qu’il faut changer de réglage ou si il n’a pas le temps de le faire (MRP), il risque de ralentir son bateau ou pire, de le faire chavirer.
Il existe maintenant des systèmes appelés AST (Assisted Sail Trim) qui détectent et ajustent automatiquement les voiles du bateau (semblable à notre DDMRP). Le skipper peut alors se concentrer sur d’autres tâches sur son bateau !
Conclusion
Ce sont notamment ces différences notoires qui font basculer de plus en plus d’industriels sur un modèle de planification en flux tiré comme le DDMRP.
Vous vous demandez si vous devez mettre en place cette méthodologie chez vous ? Ça se discute ensemble ! Le DDMRP n’est pas non plus la baguette magique à tous les problèmes industriels, construisons ensemble une feuille de route adaptée à vos problématiques !
Articles qui pourraient vous intéresser également :