
Le DDMRP, méthode de planificationinnovante, s’appuie sur 5 piliers clé pour sécuriser le flux face aux aléas du marché, tout en synchronisant votre Supply Chain avec la demande réelle.
Déroulé de l'article
Rappel : La méthode Demand Driven en quelques mots
Le DDMRP est une méthode de planification et d’exécution de la production née aux Etats-Unis dans les années 2010 pour répondre aux nouveaux enjeux des entreprises : évoluer dans des environnements de plus en plus Complexes, Volatiles, Complexes, Ambigus (Lire l’article sur le monde VUCA). Dans ce contexte, où les méthodes de gestion traditionnelles ont atteint leurs limites, cette méthodologie Demand Driven permet de maximiser les taux de service, tout en réduisant les stocks et les surcoûts inutiles. Cette méthode s’appuie sur 5 piliers clés.
Les 5 étapes du DDMRP
1. Le positionnement stratégique des stocks tampons
La première étape de la méthode Demand Driven Material Requirement Planning (DDMRP) consiste à placer des stocks de découplage à des endroits stratégique de la Supply Chain, afin de sécuriser et d’accélérer le flux.
Prenons un exemple plus concret : le skipper qui part en régate. Pour arriver le plus vite et avoir des chances de gagner la course, il ne va pas pouvoir s’arrêter dans chaque port. Stratégiquement, il vaut donc mieux qu’il parte sur la ligne de départ avec l’ensemble de ses vivres, de ses voiles et autres ressources directement sur le bateau.
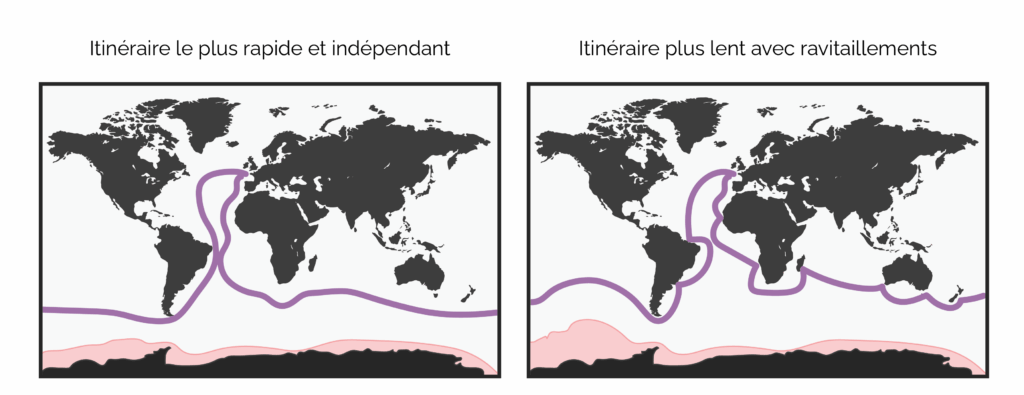
Le découplage est l’art de positionner un stock découplage aux bons endroits dans la Supply Chain pour réduire l’impact de la variabilité amont et aval, comme les retards fournisseurs, les changements erratiques de la Demande client ou les pannes machines. Le bon positionnement de ces stocks (choix très stratégique) nécessite ainsi une analyse approfondie de vos flux et un travail de segmentation Supply Chain.
Pour mieux comprendre les éléments à prendre en compte pour positionner un stock tampon, consultez notre article : DDMRP: Qu’est-ce qu’un Buffer ?
2. Le dimensionnement des points de découplage
Une fois que le positionnement des stocks de découplage est fixé, la seconde composante de la méthodologie DDMRP est de les dimensionner.
Un stock trop important encombrerait inutilement des emplacements dans les racks, immobiliserait du cash, et coûterait potentiellement très cher en coûts d’obsolescence. À contrario, un stock trop faible entraînerait des ruptures et des surcoûts sous la forme de transports urgents, d’heures supplémentaires ou de désorganisation de la production. Avec la méthodologie DDMRP, les stocks aux points de découplages sont calculés au plus juste, ni trop, ni pas assez.
En mer, tout est aussi une question de juste dosage. Une voile bien réglée, qui prend bien le vent, peut faire accélérer le bateau. Au contraire un mauvais réglage, une taille de voile non adéquate peut entraîner le renversement du voilier. C’est tout le rôle du skipper (l’approvisionneur) de bien paramétrer son outil !
Consultez nos formations DDMRP pour apprendre à maîtriser les notions de dimensionnement et positionnement des stocks de découplage
3. L’ajustement dynamique des Buffers de stocks
L’étape suivante consiste à ajuster dynamiquement ces stocks de découplage en fonction de l’évolution du contexte du marché. Il existe deux manières :
- L’ajustement calculé (automatiquement) : cet ajustement, effectué quotidiennement par un outil DDMRP, se fait systématiquement par exemple selon l’évolution des ventes ou des lead-times. Les skippers en mer peuvent par exemple maintenant faire appel à des AST (Assisted Sail Trim) qui adaptent automatiquement le réglage des voiles selon les conditions météorologiques en temps réel.
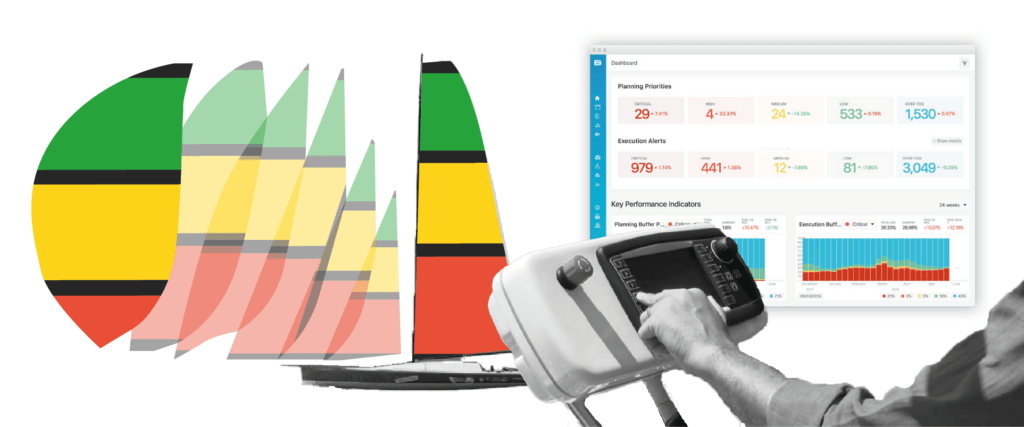
- L’ajustement planifié : cet ajustement fait appel à toute la connaissance du planificateur sur ses articles et sa Supply Chain. Il va ainsi ajuster ses Buffers selon des événements anticipés, comme par exemple des saisonnalités, des promotions, des arrêts de lignes pour maintenance, le nouvel an chinois, la fin de vie d’articles, le lancement de nouveaux articles, etc.
Autre comparaison avec notre ami skipper : lors des courses en solitaire, il va programme un certain réglage de voile, par exemple assez sécuritaire s’il doit se concentrer sur une manœuvre compliquée à côté ou si il souhaite dormir quelques minutes.
Testez la compatibilité de votre entreprise et de votre marché au DDMRP
4. La planification tirée par la demande
Avec la 4ème étape du DDMRP vient la planification opérationnelle « tirée par la demande » des ordres de production ou d’approvisionnement.
La génération de ces ordres selon la méthode DDMRP est basée sur une innovation : l’équation de flux disponible. Elle est calculée à partir du stock disponible, des encours de production ou d’appro, de la demande à servir et des pics de demande déjà connus.
Cette équation de flux, calculée quotidiennement, donne une position de flux qui détermine si un réapprovisionnement doit ou non être lancé, et de quelle quantité : vous êtes dans la zone verte du Buffer ? Tout va bien, vous pouvez faire autre chose. Vous êtes dans la zone jaune ou zone rouge? Vous devez repasser une commande pour revenir « au top du vert ». Simple non ?
En voile c’est le même principe : le skipper va surveiller les prévisions météorologiques pour savoir quelle voile emporter durant une course. Mais une fois en route, c’est le bien le vent mesuré et constaté en temps réel qui va orienter le choix de la voile à monter et qui va déclencher un réglage.
5. L’exécution et le pilotage de façon visuelle
La cinquième et dernière composante du DDMRP est l’exécution « Demand Driven ». La planification est une chose, la vraie vie en est une autre. Comment prioriser mes OF ? Comment savoir si tel aléa (retard fournisseur, panne machine, problème qualité…) va compromettre ou non mes engagements clients ? La méthodologie du DDMRP prévoit pour cela deux types d’alertes : les alertes de statut de Buffer et les alertes de synchronisation :
- Les alertes de statut de Buffer, pour identifier les problèmes de stocks, actuels ou à venir
- Les alertes de synchronisation, pour piloter les flux entre deux stocks de découplage
C’est un peu comme en navigation, le skipper va régler ses voiles selon les conditions météorologiques ressenties mais va ensuite surveiller comment réagit son bateau. Il reste agile, prêt à réajuster n’importe quel paramètre si son bateau frôle le chavirement ou ralentit trop.
Voilà, votre modèle opérationnel DDMRP tiré par la demande est en place. Il ne reste plus qu’à le faire vivre et l’améliorer dans une logique de progrès continu. Pourquoi pas le connecter à votre stratégie d’entreprise au travers du processus S&OP (PIC) !
Articles qui pourraient vous intéresser également :